Have you found yourself wondering, how are cigars made? Well, the finest cigars might come from Cuba, but cigar manufacturers are all over the world. Besides, centres of cigar cultivation exist in areas like Java, Russia, Massachusetts, and the Philippines.
There are also many cigar factories in America with most of them existing in Connecticut, Pennsylvania, and New York. However, the process of manufacturing cigars is not that different.
For instance, the finest premium cigars are still made by hand, even though most are made by machines partially or entirely. Additionally, the primary raw material for every cigar is the tobacco leaf.
But, if you want the finest cigar tobacco, then look for the varieties that are grown in Jamaica, Cuba, and the Dominican Republic. These are also the regions where you can get the best gifts for your cigar aficionados.
Having said that, let’s answer the question, how are cigars made, by first diving into cigar raw materials.
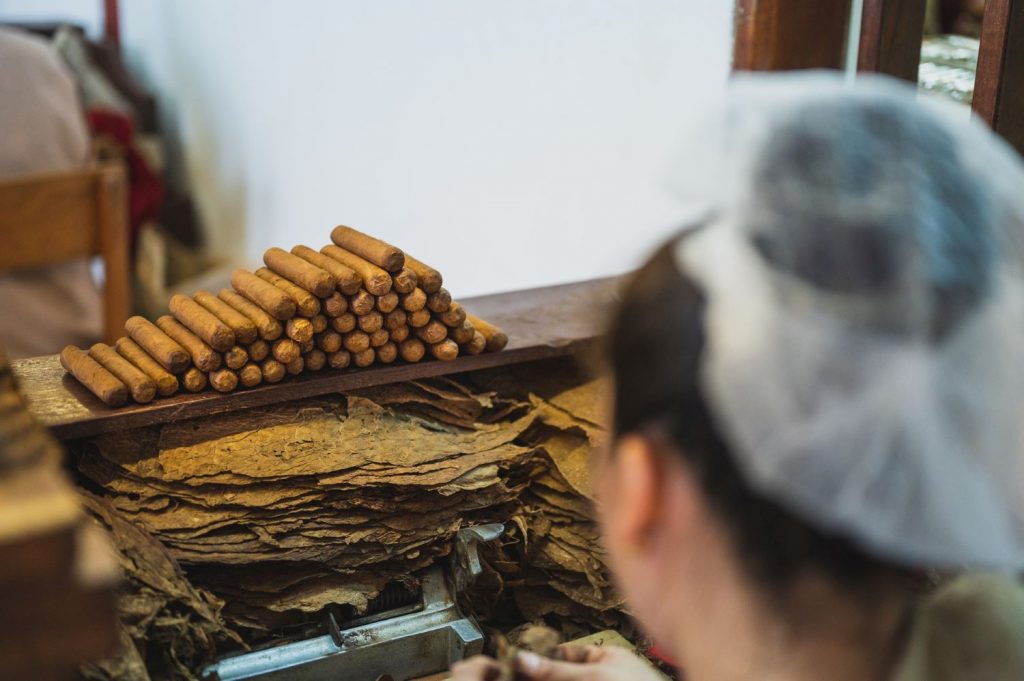
The Raw Materials
If you want to make your cigar, you’ll need three types of tobacco leaves as the raw materials. These include:
- The filler leaf – the small and broken tobacco leaves
- The binder leaf – these are whole tobacco leaves
- The wrapper leaf – large and finely textured tobacco leaf
You don’t have to get the best quality tobacco leaf to make the binder because its appearance is not a concern. However, the wrapper needs to have a uniform appearance because it represents the outside of the cigar.
You’ll find cigars made from tobacco plants from the same region. But others are made from tobacco leaves from different regions. For instance, you can find a cigar whose wrapper is from a high-quality Cuban leaf while the filler is from another regions’ low-quality tobacco.
Apart from the harvested tobacco, other raw materials needed to make cigars include flavouring agents, tasteless gum to keep the wrapper together, and the paper used as the cigar band. It is important to note that machine-made cigars use a homogenized tobacco leaf for the wrapper and binder.
A homogenized tobacco leaf is made from pulverized tobacco leaf scraps mixed with gum. They are then rolled into sheets to form the wrappers and binders. Now that you know the materials needed to make a cigar, let’s look at the manufacturing process:
Manufacturing A Cigar
The right type of tobacco will give you the best cigars to smoke. Nevertheless, the manufacturing process also affects the type of cigar flavour and burn. So, how are cigars made? They are taken through the following processes:
Cultivation
Tobacco plants are usually seeded indoors for about 6 to 10 weeks before they are taken into the fields. Once in the fields, the plants take several months to mature.
Curing
Once the tobacco plants are ready for harvest, they are dried yellow or golden brown. Then they are cured by stringing the plants on narrow strips of wood known as laths. These laths are hung from the ceiling of a curing barn with perfect ventilation.
Fermentation
After curing, the tobacco leaves are sorted by size and color. These leaves are then tied into bundles and are stored in boxes for 6 months to 5 years. During this fermentation period, the leaves undergo chemical processes causing the aroma and the taste of the tobacco leaf to develop.
Stripping
Smoking a cigar with an even burn is only possible once the filler leaves have no stem or main vein. This is what is called stripping, after which the leaves are wrapped on bales and stored for additional fermentation. Then just before the cigar manufacturing process begins, these leaves are steamed to restore humidity and sorted one final time.
Wrapping
Considered the most challenging cigar manufacturing step, the partially completed cigar is placed in a wrapper leaf. A rounded knife called a chaveta is then used to trim the irregularities in the cigar filler. Finally, the cigar roller rolls the wrapper leaf around the cigar filler and binder at least three and a half times. The result is secured with vegetable paste at the end of the wrapper.
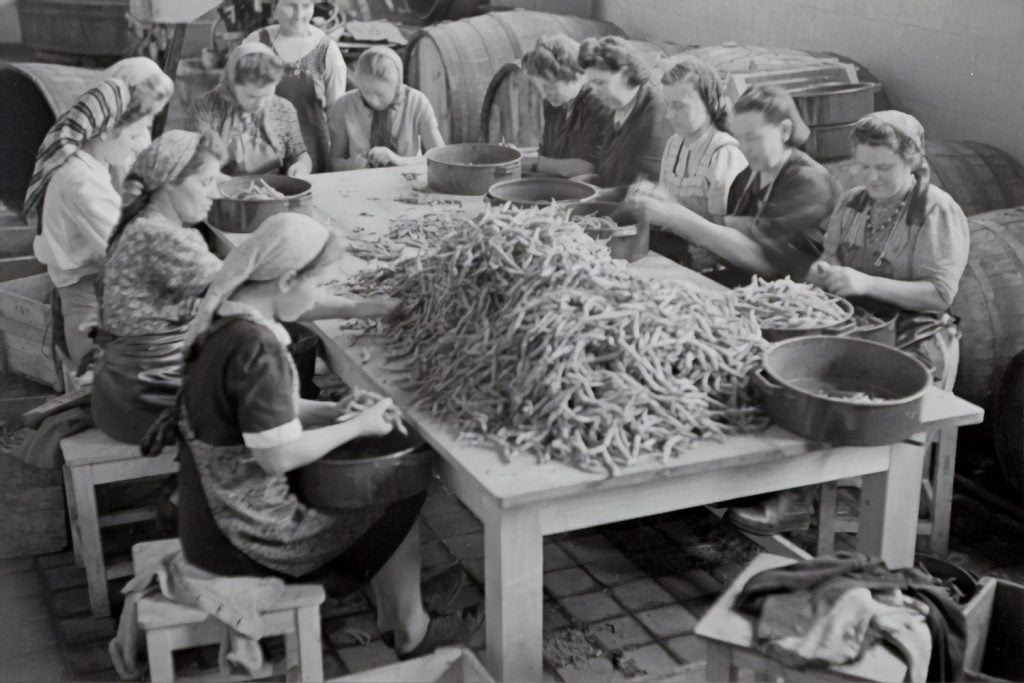
Hand rolling
Cigars that are rolled by hand are the finest. The filler is also packed evenly and the wrapper has an even spiral around the cigar. Hence, these cigars burn smoothly.
Machine rolling
Here, tobacco leaves are fed into a feed belt, by one worker, which is between guide bars specially adjusted to the length of the cigar. The machine then bunches the leaves to make the filler. Another worker places the binder on the binder die where it is held down by suction and the machine cuts it to the desired size. The machine then rolls the binder around the filler. A third worker places the wrapper leaf on the wrapper die where the cigar drops on the wrapper for more rolling. The fourth and final worker insects the cigars before placing them in a tray.
Inspection
Cigar inspection happens throughout the cigar manufacturing process. That is also why sorting takes place after curing and fermentation to ensure quality control. The finished products are also checked for consistency in diameter, size, weight, and draw. Any imperfections on the wrapper are also considered. After inspection, the cigars are collected in bundles of 50, labelled, and sent for storage.
Storage
Temperature and humidity levels are always kept at ideal levels in marriage rooms where the cigars are stored in cedar drawers, bins, or shelves. The cigars can stay here for three weeks to one year. Storage also allows the wrapper to dry, which shrinks and compresses and solidifies the cigar in response. The result is a slow-burning and dense finished product.
Seasoning
For further ageing, some manufacturers like to inter-marry the cigars in the seasoning room. Here, different cigars with different tastes and aromas are kept in a room for a period. Since the tobacco absorbs the aromas and oils of its surrounding, these cigars end up with the same taste and smell.
Conclusion
There is a lot that happens in a cigar factory. Nevertheless, the process of manufacturing cigars remains quite similar. However, different brands incorporate different flavors and seasonings to give off a unique company taste. But remember, if you want the best Cuban cigar in the market, ensure it is hand-rolled.